Skills Gap Analysis | Capability Solutions
Professional manufacturing capability evaluation combines systematic competency assessment with comprehensive development planning, ensuring precise alignment with operational requirements through established quality-assured channels. Through structured verification frameworks and continuous monitoring protocols, each analysis delivers measurable improvement while maintaining clear documentation through secure systems."
Technical Capability Framework
Technical competency assessment
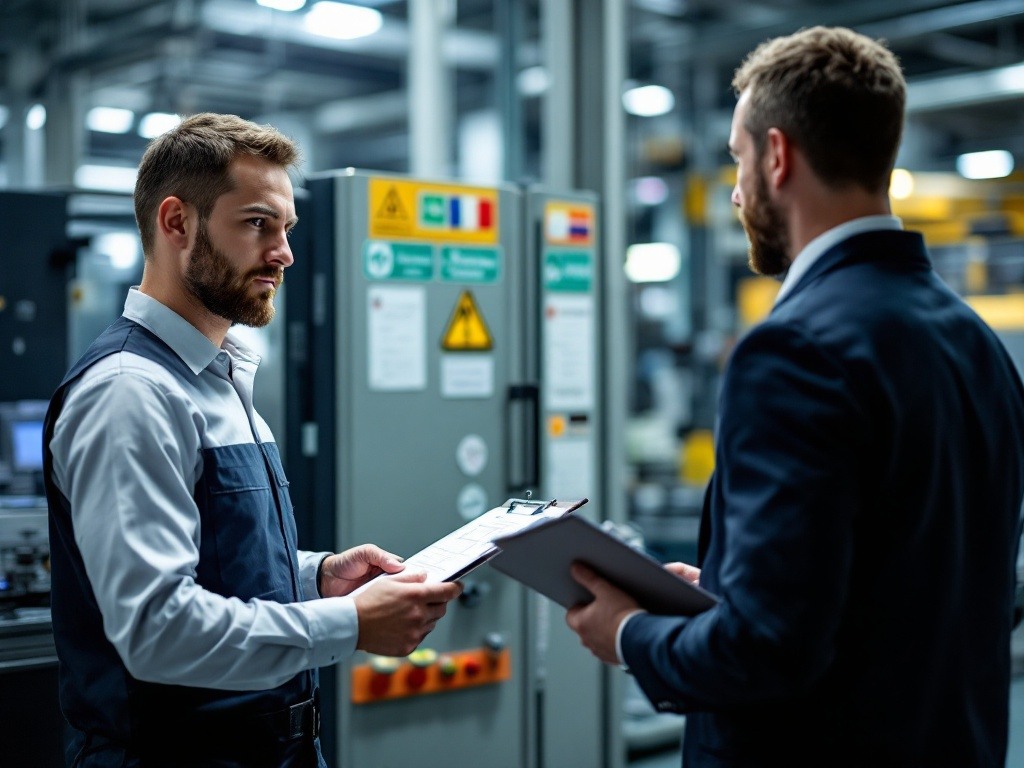
Manufacturing skills verification
Systematic evaluation of practical manufacturing abilities encompassing detailed assessment of process understanding, material handling proficiency, and production technique application. Our verification protocols examine specific operational capabilities including machine setup procedures, quality control implementation, and adherence to manufacturing specifications.
Equipment proficiency evaluation
Comprehensive assessment of operator capabilities across manufacturing machinery, examining detailed aspects of equipment setup, operational control parameters, maintenance awareness, and troubleshooting abilities. Our evaluation includes practical demonstrations of technical competency across various production scenarios.
Quality standard compliance
Detailed verification of adherence to established manufacturing quality protocols, measuring consistency in product specifications, process standards, and documentation requirements. Our assessment examines understanding of quality control procedures, inspection techniques, and corrective action protocols.
Development needs identification
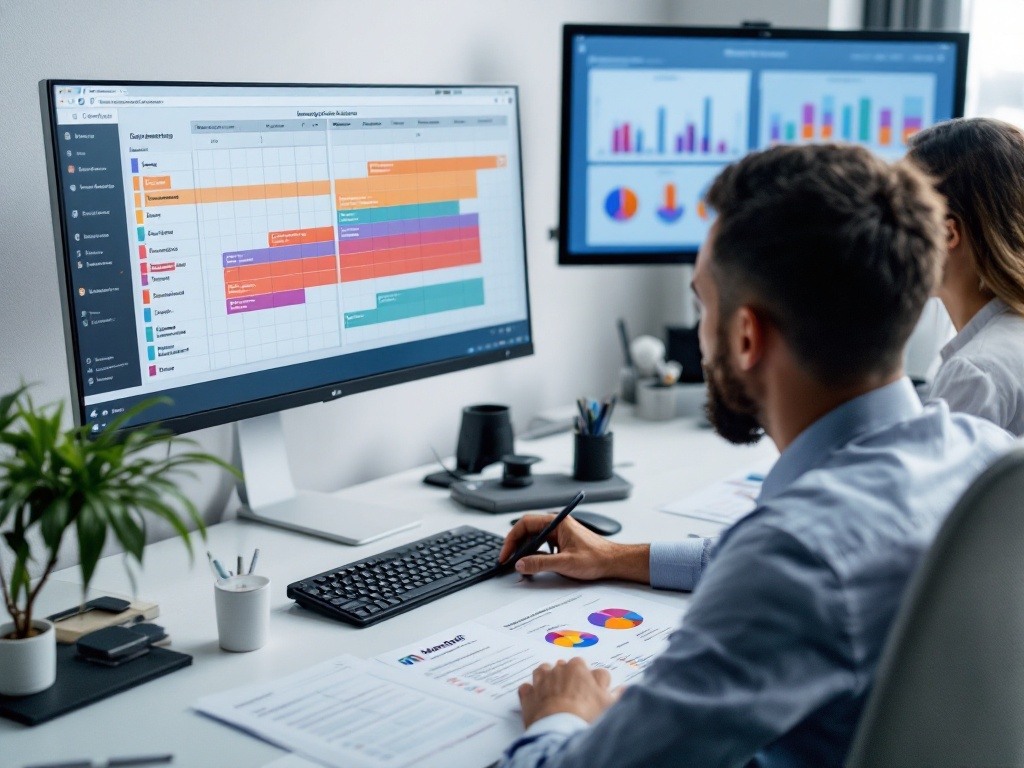
Current capability mapping
Systematic documentation of existing technical competencies across manufacturing functions, creating detailed profiles of present skill levels, operational expertise, and specialized knowledge areas. Our mapping process captures specific abilities within each production role.
Required competency assessment
Comprehensive analysis of essential manufacturing capabilities needed for optimal production performance, examining specific technical requirements, operational standards, and quality maintenance protocols. Our assessment establishes clear benchmarks for required skill levels.
Performance gap analysis
Detailed identification of specific areas where current capabilities differ from required manufacturing competencies, examining technical skills, operational knowledge, and quality standards. Our analysis provides precise measurement of development requirements.
Training pathway planning
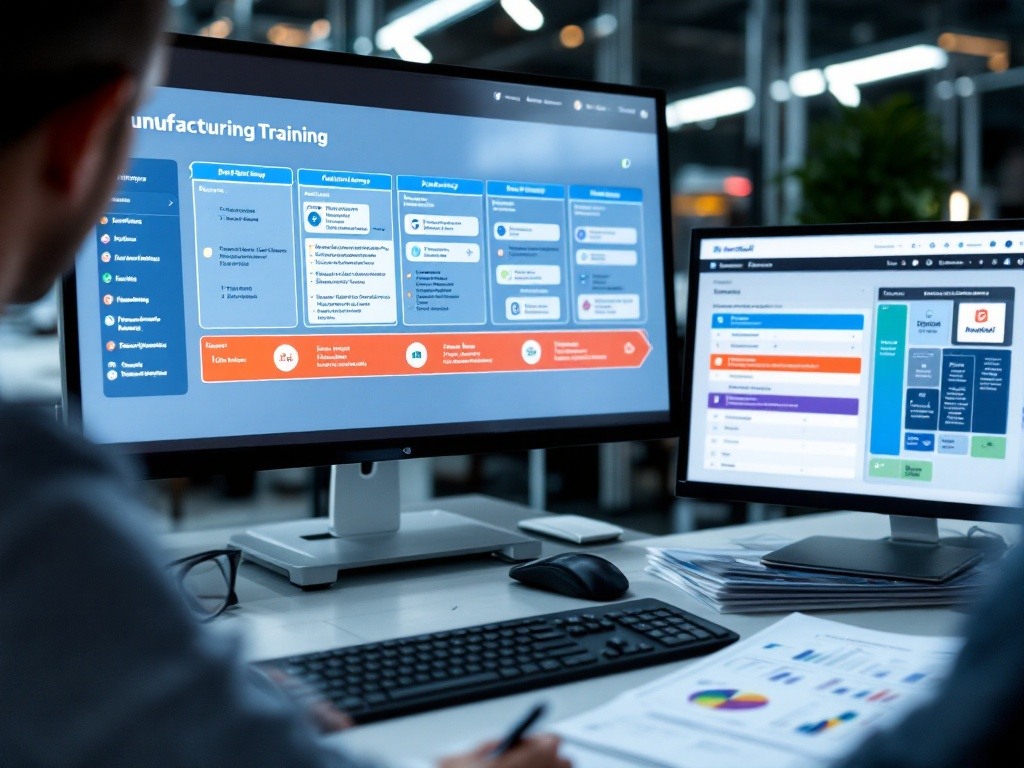
Skill development roadmaps
Strategic creation of structured learning pathways designed to enhance specific manufacturing capabilities, incorporating targeted training interventions, practical assessments, and progression milestones. Our roadmaps outline clear development sequences.
Resource requirement planning
Comprehensive identification of necessary training materials, equipment access requirements, supervision needs, and time allocations for effective skill development. Our planning ensures availability of all resources needed for successful implementation.
Implementation timelines
Strategic establishment of realistic development schedules considering production demands, resource availability, and operational constraints. Our timeline planning includes specific milestones, progress reviews, and completion targets.
Service Excellence Framework
Complimentary consultation service
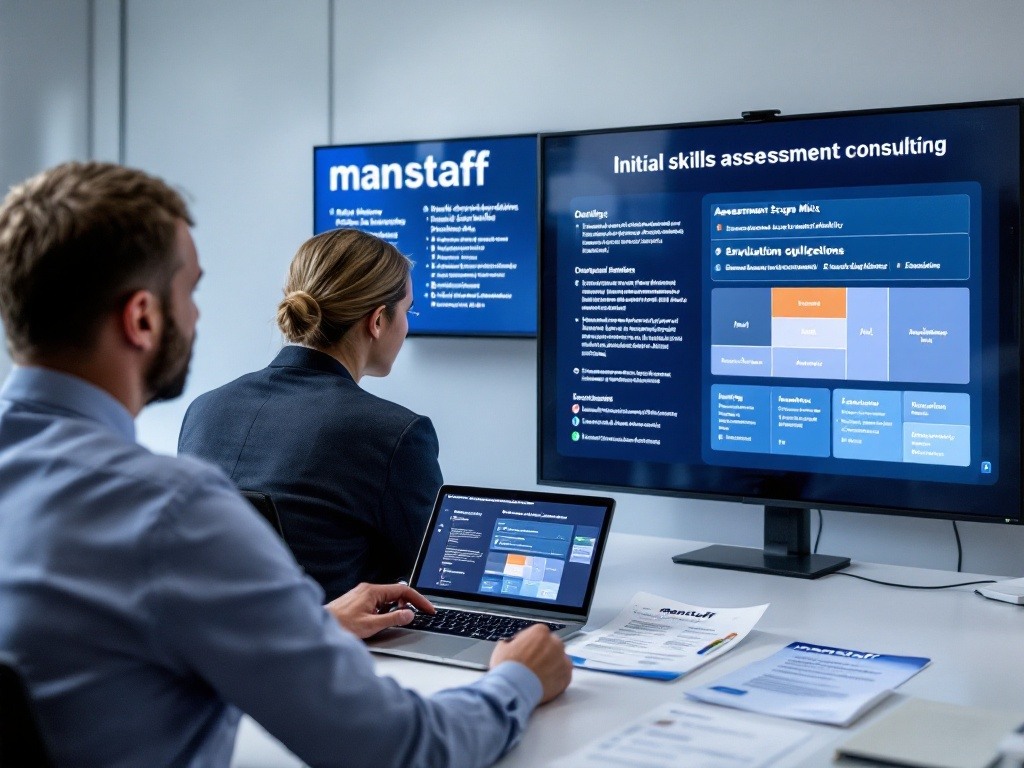
Manufacturing requirement evaluation
Detailed initial assessment of specific production needs examining critical operational capabilities, quality standards, and technical requirements. Our evaluation process identifies key areas requiring capability enhancement.
Assessment scope definition
Precise delineation of evaluation parameters including specific roles, processes, equipment requirements, and quality standards. Our scope definition ensures comprehensive coverage of all relevant manufacturing aspects.
Development objective setting
Strategic establishment of clear capability enhancement goals aligned with manufacturing quality standards, efficiency targets, and operational requirements. Our objective setting creates measurable development outcomes.
Systematic capability collection
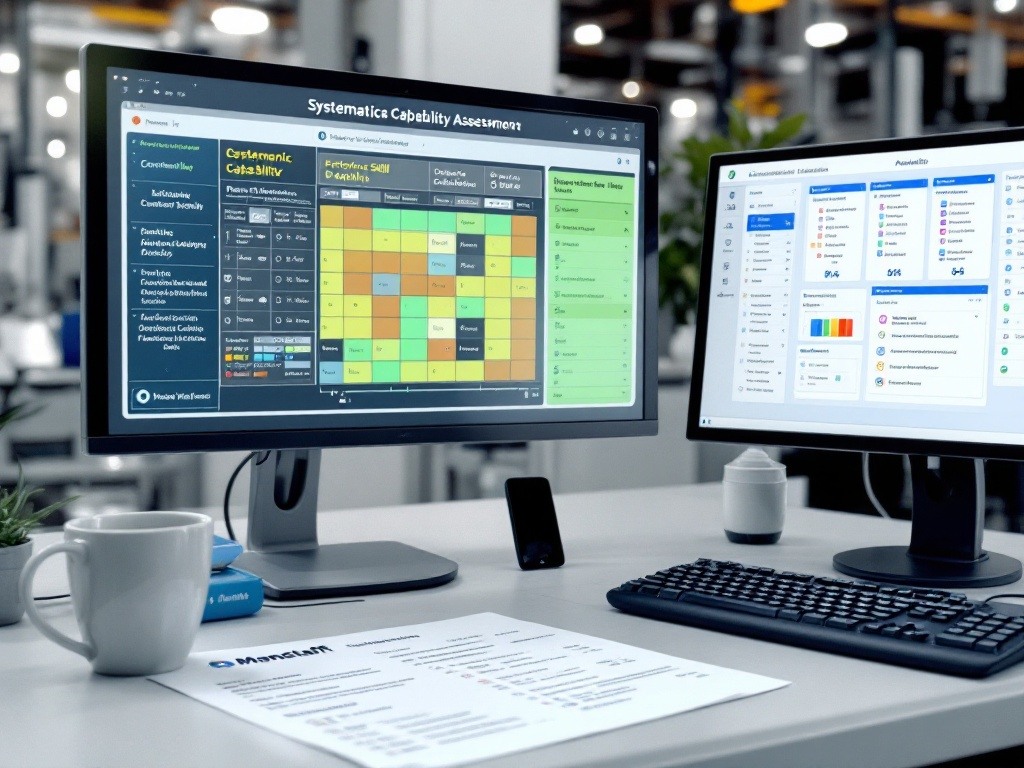
Technical skill verification
Comprehensive practical assessment of specific manufacturing abilities through structured observation, performance testing, and capability demonstration. Our verification process examines actual operational competency.
Competency data acquisition
Systematic collection of detailed capability information through comprehensive evaluation of operational performance, technical knowledge, and practical application. Our data gathering ensures complete understanding of current abilities.
Performance monitoring
Continuous tracking of skill application and development progress within production environments, examining consistency, quality, and efficiency improvements. Our monitoring process provides regular capability assessments.
Comprehensive analysis protocols
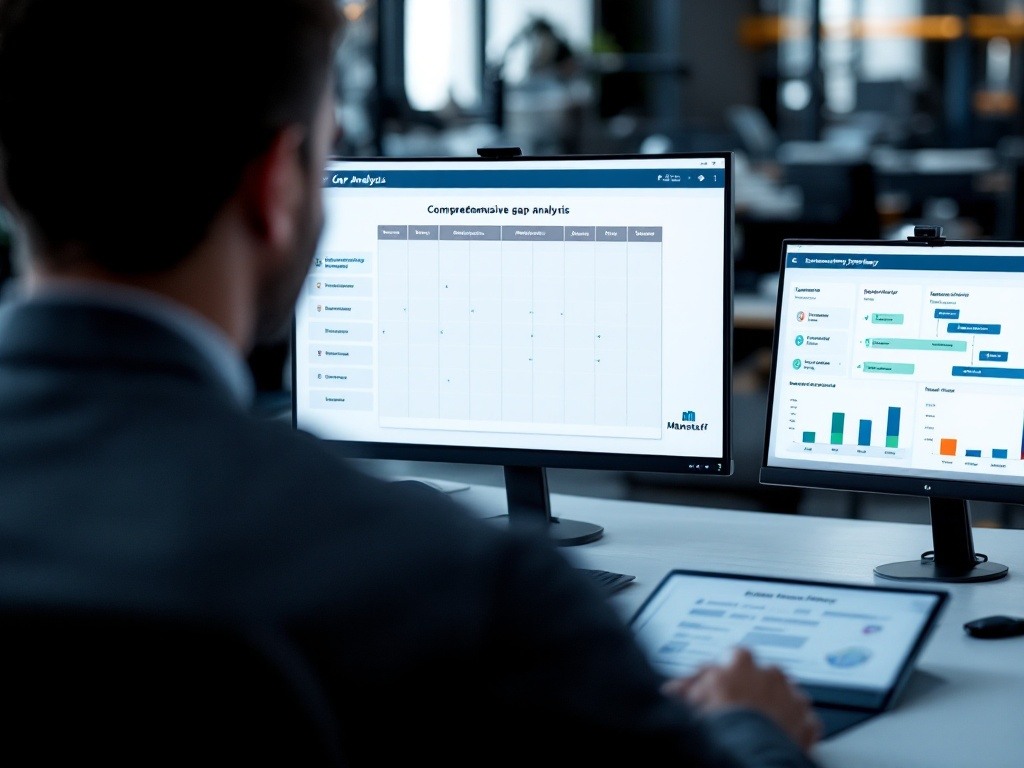
Gap identification methodology
Advanced structured approach to recognizing specific areas requiring capability enhancement, utilizing systematic analysis tools and established evaluation frameworks. Our methodology ensures precise identification of development needs.
Development need prioritization
Strategic ranking of identified skill gaps based on operational impact, development urgency, and resource requirements. Our prioritization process ensures optimal allocation of development resources.
Improvement pathway planning
Comprehensive design of systematic approaches to address identified capability gaps, incorporating specific interventions, progress measurements, and success criteria. Our planning ensures effective development implementation.
Clear documentation provision
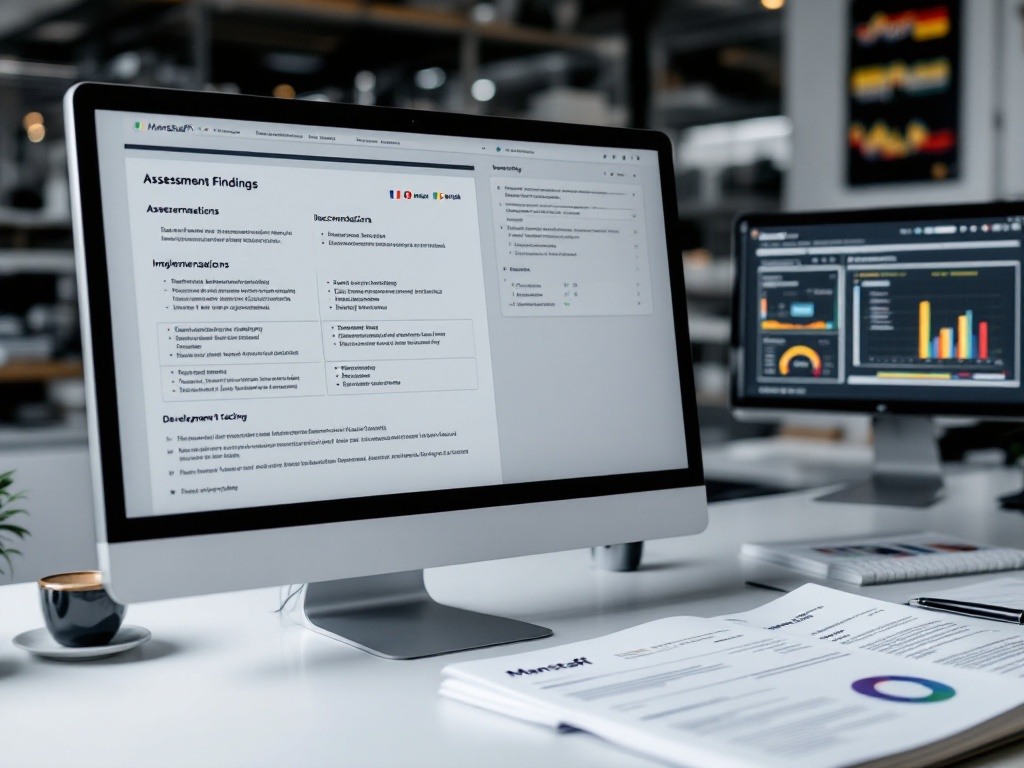
Assessment report generation
Professional creation of detailed documentation outlining current capabilities, identified gaps, and development needs. Our reports provide clear visualization of assessment findings through structured presentation formats.
Development recommendations
Strategic formulation of specific actions required to enhance identified manufacturing capabilities, including detailed intervention strategies, resource requirements, and expected outcomes. Our recommendations provide clear implementation guidance.
Implementation guidance
Comprehensive provision of detailed instructions for executing recommended development initiatives, including specific steps, resource allocation, and progress monitoring protocols. Our guidance ensures effective execution of improvement plans.